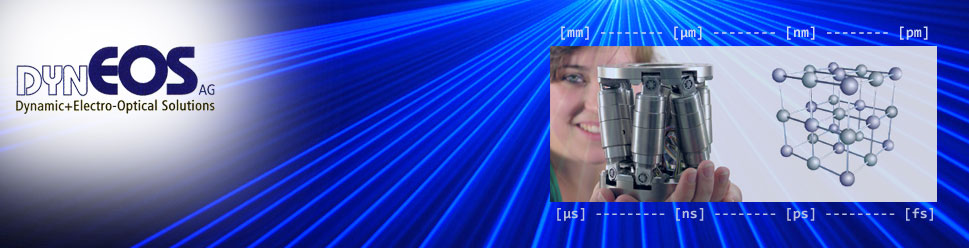
Nanopositioning and Nanomeasuring Machine from DYNEOS AG
Your specialist for Laser, Photonic & Nanotechnology in Switzerland
& Liechtenstein
The
Nano Positioning and Nano Measuring Machine is used for the three-dimensional coordinate measurement
in a range of 25 mm x 25 mm x 5 mm with a resolution of 0.1 nm. Its unique sensor arrangement provides
Abbe error-free measurements on all three coordinate axes. The measurement axes of three miniature plane
mirror interferometers for length measurements intersect with the contacting point of the probe sensor
with the measuring object at a single point. The measuring object is placed directly on a movable mirror
corner.
|
The position of this mirror corner is monitored by the three fixed Series SP 500 miniature interferometers.
The mirror corner is positioned by a three axis electrodynamic driving system.
Any angular deviations during the positioning process are measured and corrected by two angle sensors.
The light of three stabilized lasers are guided from the electronics unit to the interferometer heads
by fiberoptic lightguides, providing a compact, thermally stable set-up of the Nano Positioning and Nano
Measuring Machine. The heart of its electronics unit is a digital signal processor (DSP) that processes
all incoming signals, controls its driving system and governs the course of measurement procedures.
|
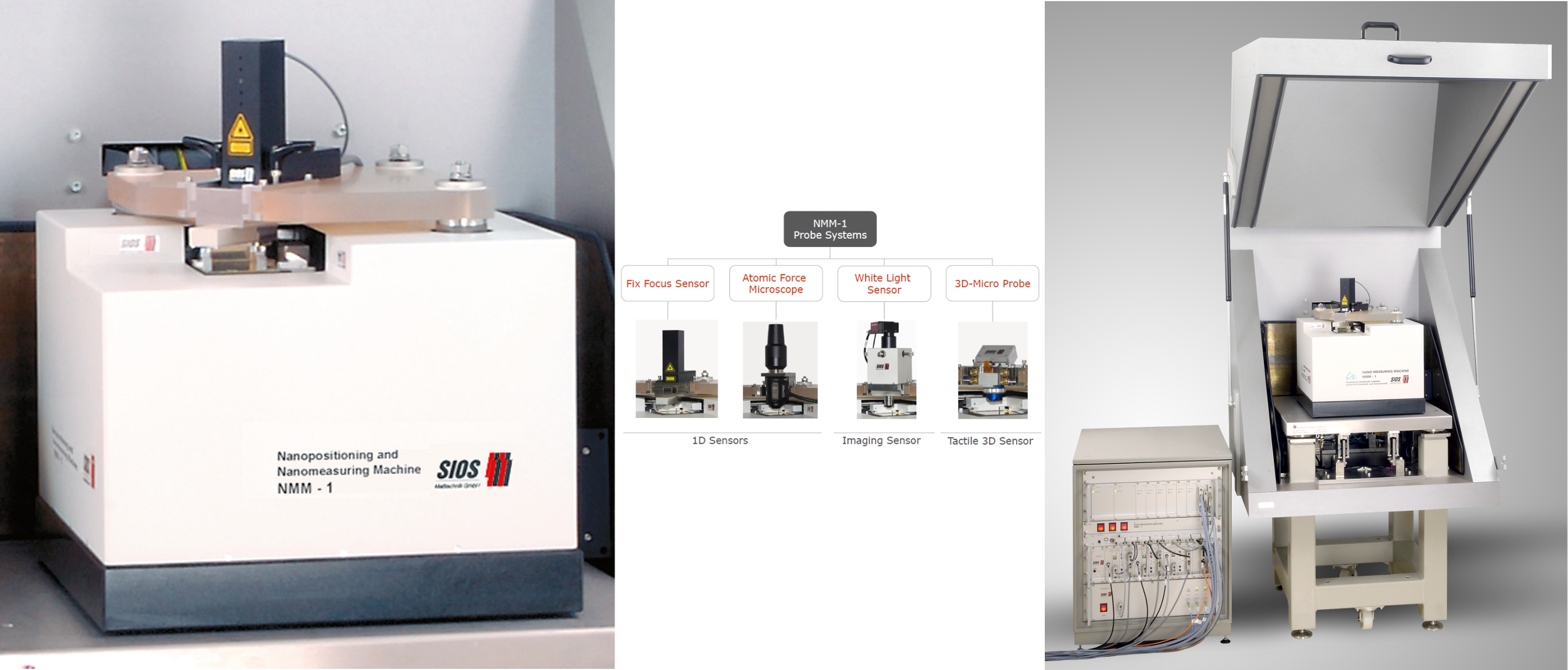
Sensors for the NMM-1
The ability to perform nanometer precision metrology is becoming increasingly influential throughout all phases of product
development and manufacture, from engineering development, through prototyping and manufacturing, to quality control, process analysis
and final inspection of components and workpieces. In particular, advances in the miniaturization of components, such as microdrives
or injection nozzles and extrusion dies, all having extremely small dimensions and subject to stringent tolerances, has driven
the need to measure three-dimensional shapes with nanometer precision. Exact machining of press tools, molding dies and optical
components with nanometer precision and optical finish has also led to demands for high-precision metrological systems,
as accurate information on the dimensions and shape of processing tools, components and workpieces is needed in those areas as well.
The NMM-1 nanomeasuring machine, developed at the Technical University of Ilmenau’s Institute for Process Measurement and Sensor
Technology and produced by Sios Messtechnik, provides the opportunity for conducting many different types of measurements.
The NNM-1 exhibits 0.1nm resolution in a measurement volume of 25 x 25 x 5 mm³ and can be equipped with various types of
tactile microprobes. The NMM-1’s excellent metrological characteristics are being exploited for calibrating transfer standards,
such as step-height standards, one-dimensional and two-dimensional lateral-displacement standards, planarity standards and roughness
standards, at several government institutions around the world.
The concept on which the NMM-1 is currently based permits using just the z-axis as the tactile-probing direction, which means
that precisely one height measurement will be correlated to every point on the xy-plane. Such measurements are termed 2.5D
surface measurements.
However, vertical surfaces can be neither detected nor analyzed using 2.5D profile measurements. Problems can also arise at steep
surface gradients that exceed a certain angle, for example as present on the curved surfaces of lenses or press tools.
In order to meet all of the demands imposed on high-precision measurements of microcomponents, the NMM-1 was upgraded by adding
3D functionality.
Structure of the NMM-1 with Laserinterferometers
3D-Measuring range of NMM-1 and technical Data
![]() |
Measuring and positioning range:
Resolution:
Probe system:
Length of the cable between measuring table and electronics unit:
Dimensions (H x W x D):
Laser safety class according to EN 60825-1: 2M |